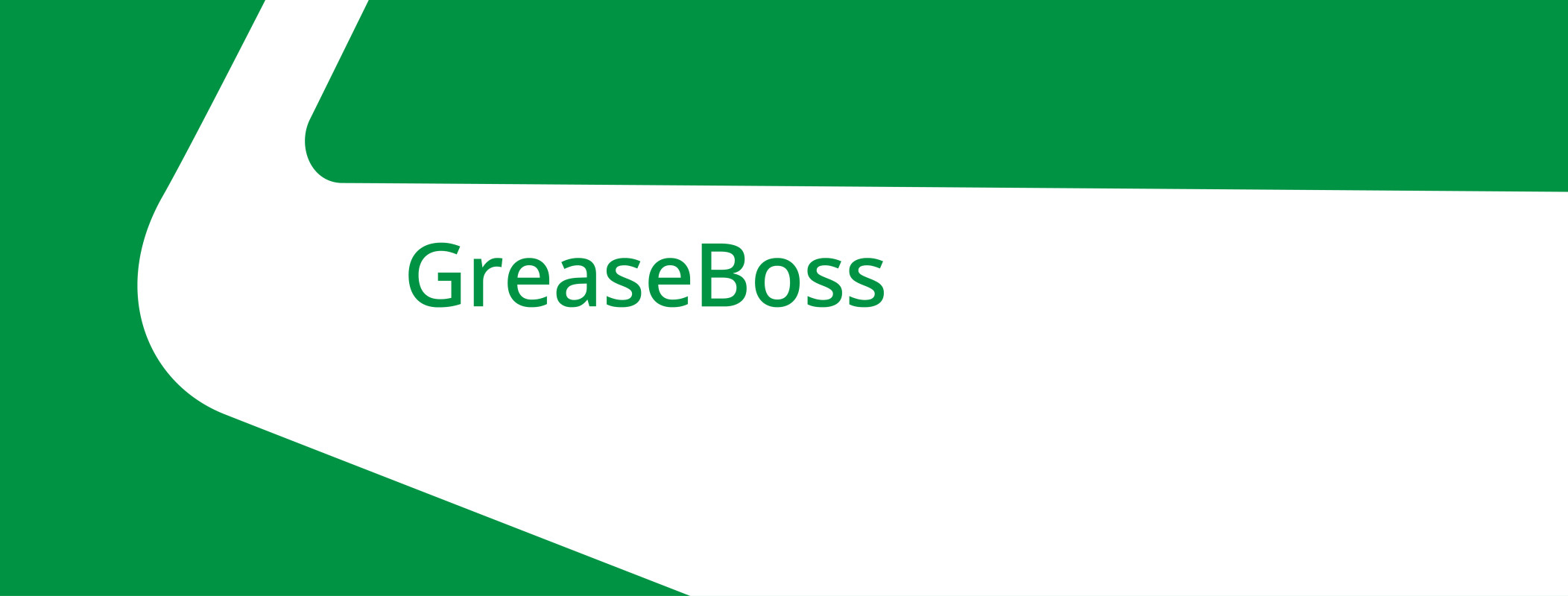
- Critical equipment failures
- Recent Failure at QLD Mine
- Minimizing Failures
- What is Greaseboss?
- The Greaseboss solution
- Verify grease flow
- Use case 1 – Eliminate The Word Bins
- Use case 2 - Eliminate The Word Monitoring
- Use case 3 – Drive Shaft Fires
- Use case 4 - fixed plant greasing
- Key benefits
- Greaseboss with Castrol customers
- The future of Greaseboss
Critical equipment failures
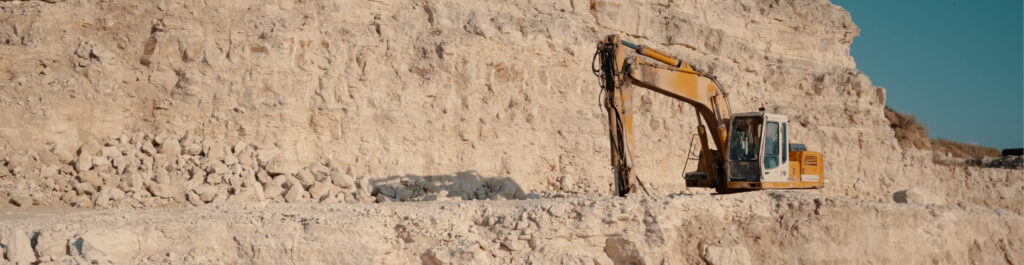
cause lost production
Large operations have 5,000– 15,000 grease points
Neglecting 1 grease point can stop production
Recent Failure at QLD Mine
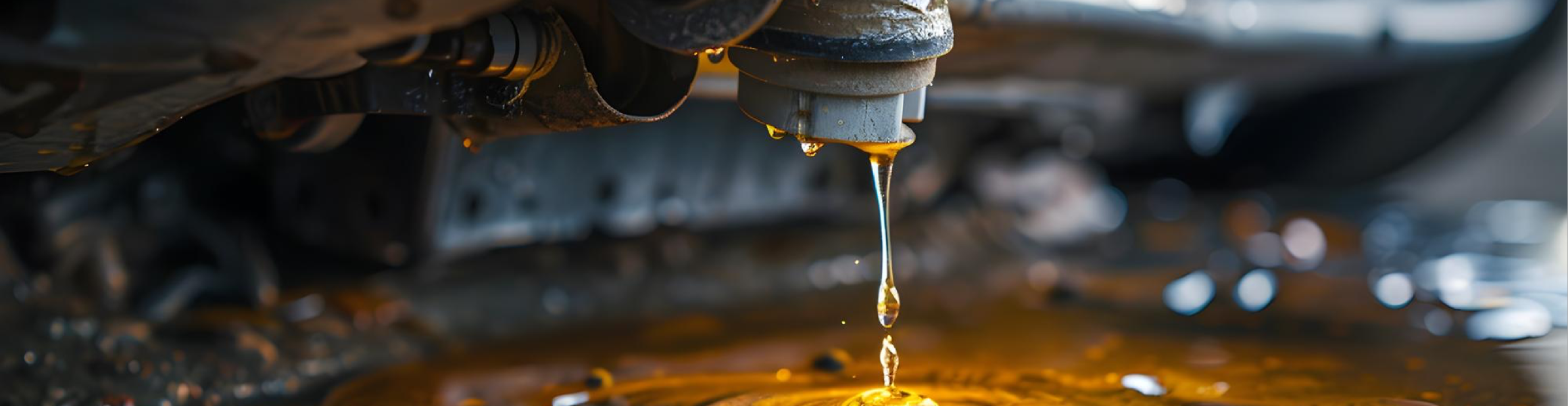
Main conveyor failed costing 43 hours of unplanned downtime
Root Cause was lack of grease on one grease point
Financial impact $34M in lost revenue + cost of repair and labour
GREASEBOSS ELIMINATES 99% OF THE RISK OF GREASE RELATED FAILURES
Provide visibility over planned vs actual greasing
activities to:
- Pinpoint the source of greasing issues
- Drive continuous improvement of site greasing activities
- Maximise equipment efficiency and uptime
- Reduce required skill level of greasers
- Track and manage down grease consumption for economical and environmental benefits
- Provide a new and unique data stream for predictive maintenance
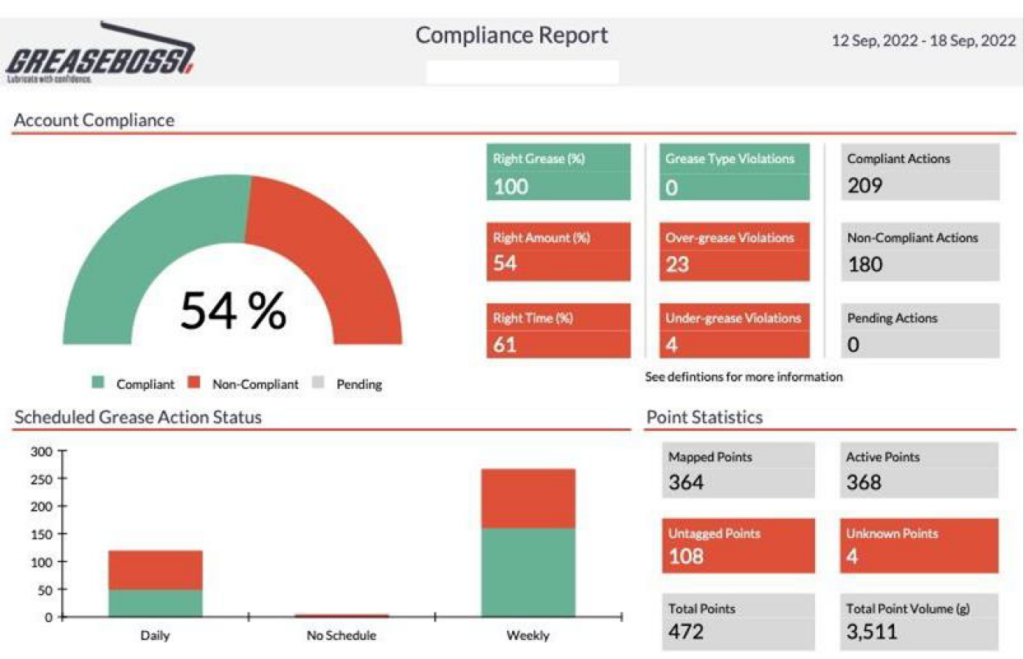
WHAT IS GREASEBOSS?
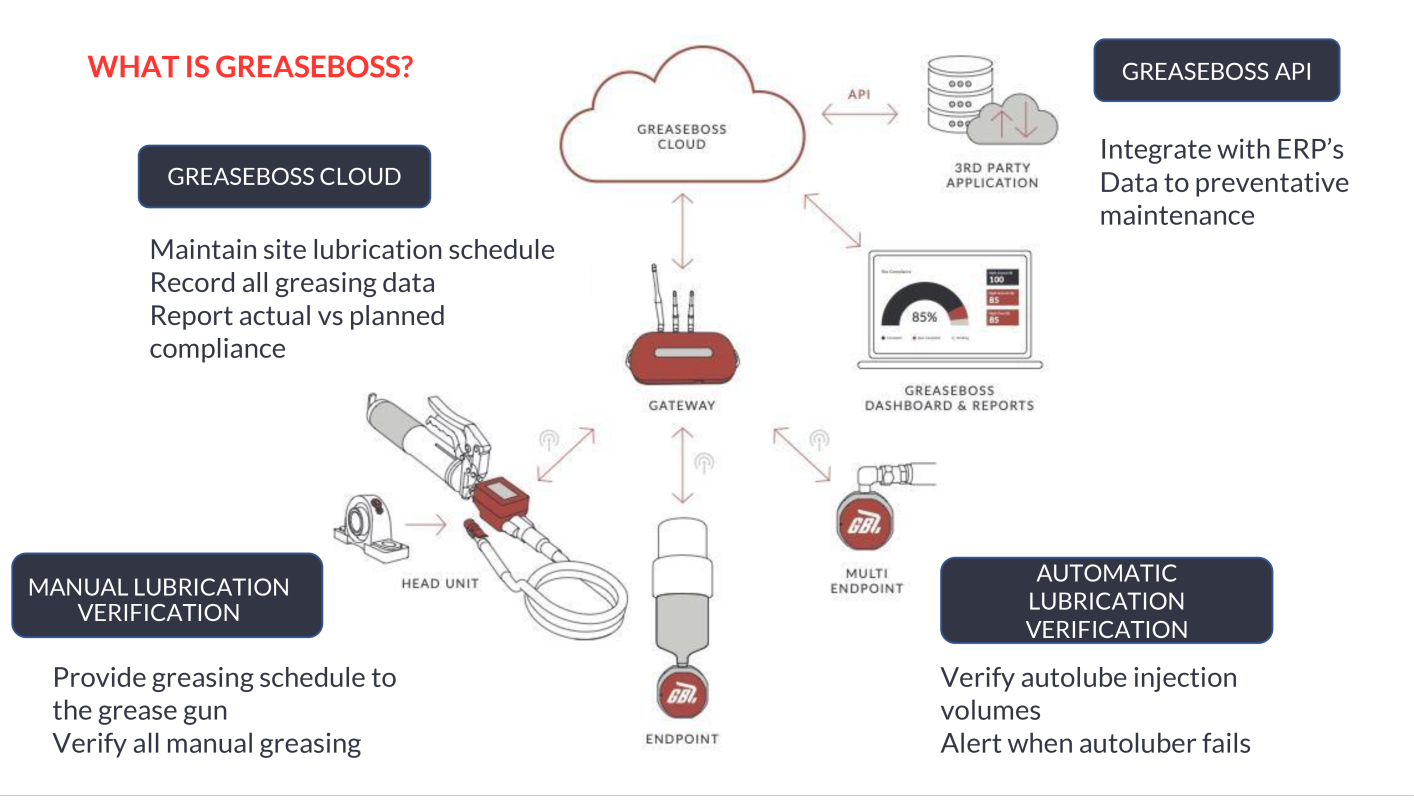
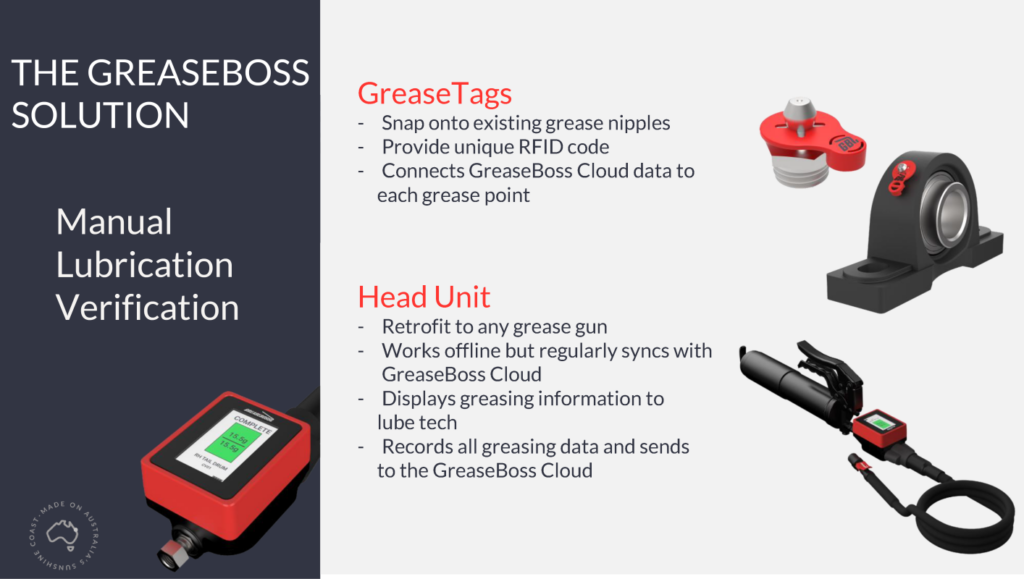
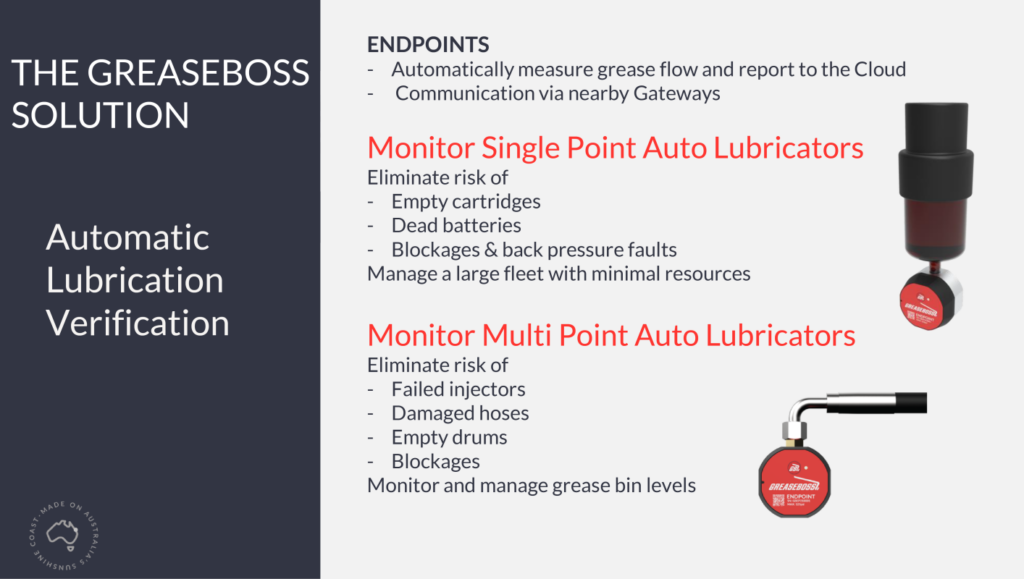
VERIFY GREASE FLOW
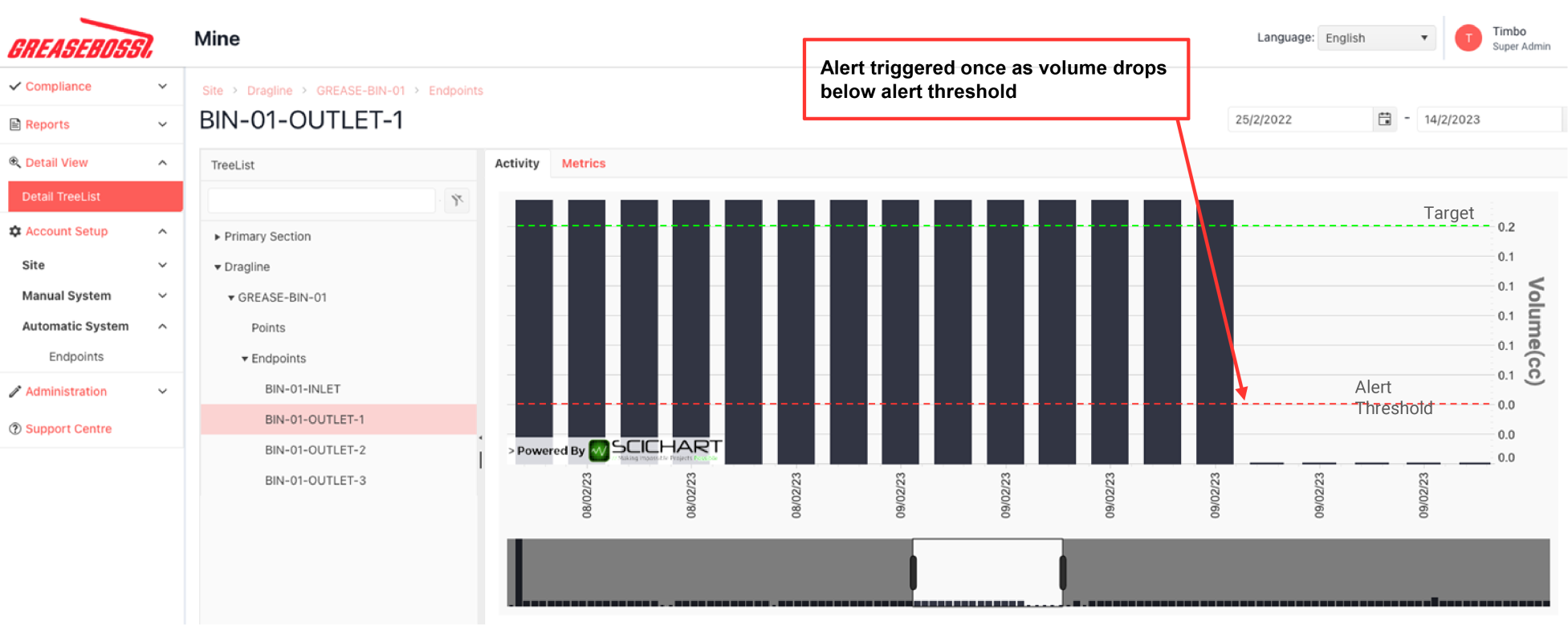
RESERVOIR MANAGEMENT
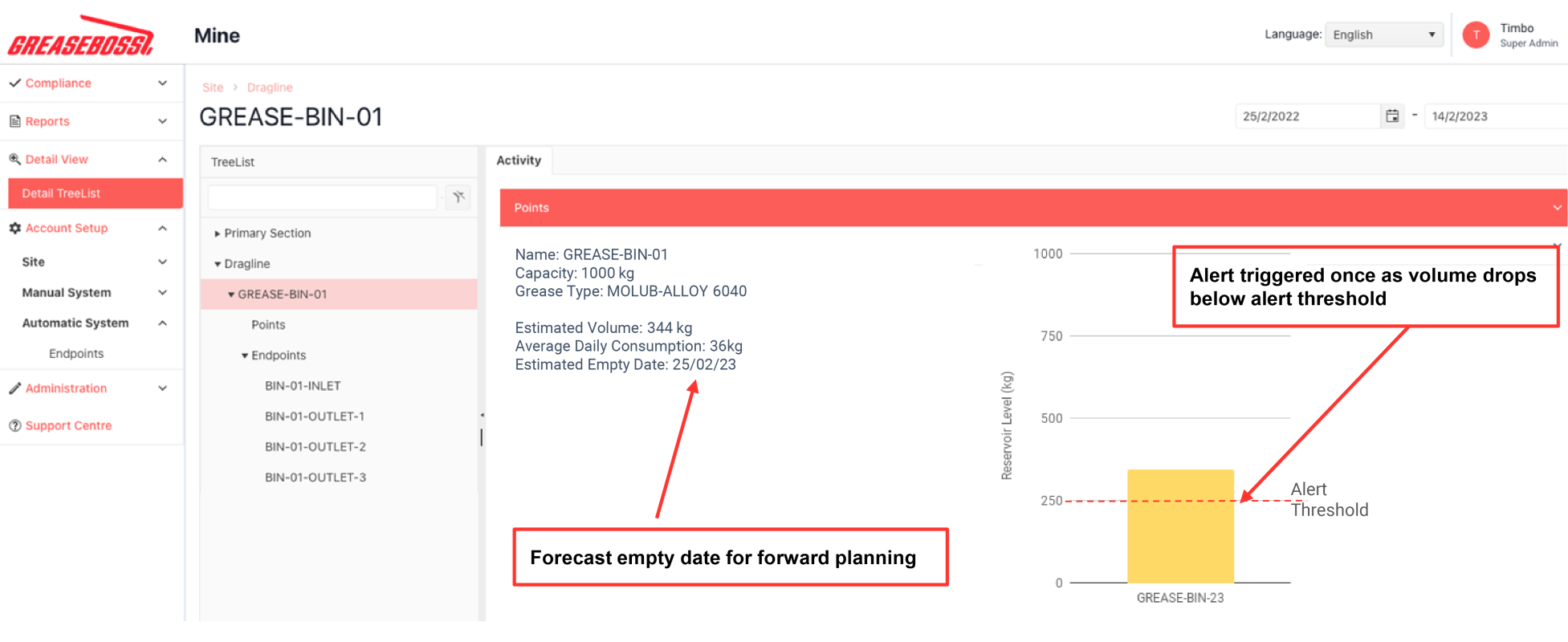
USE CASE 1 - DRAGLINE GREASE BINS
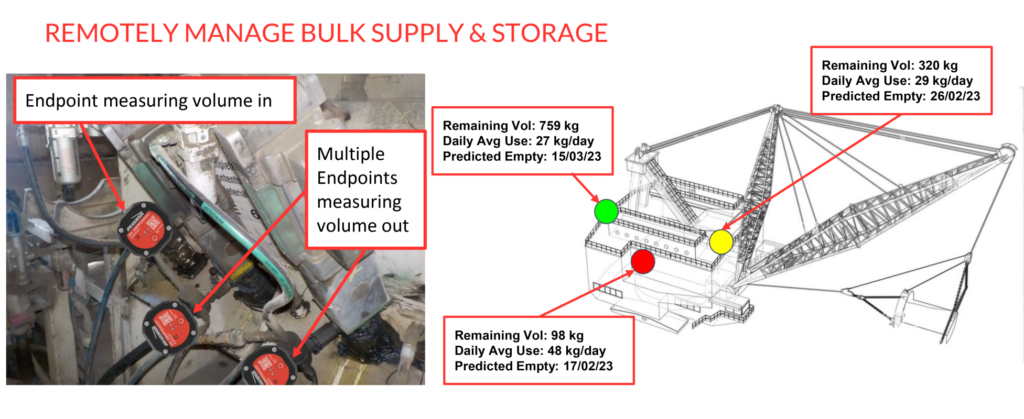
USE CASE 2 - HME INJECTOR MONITORING
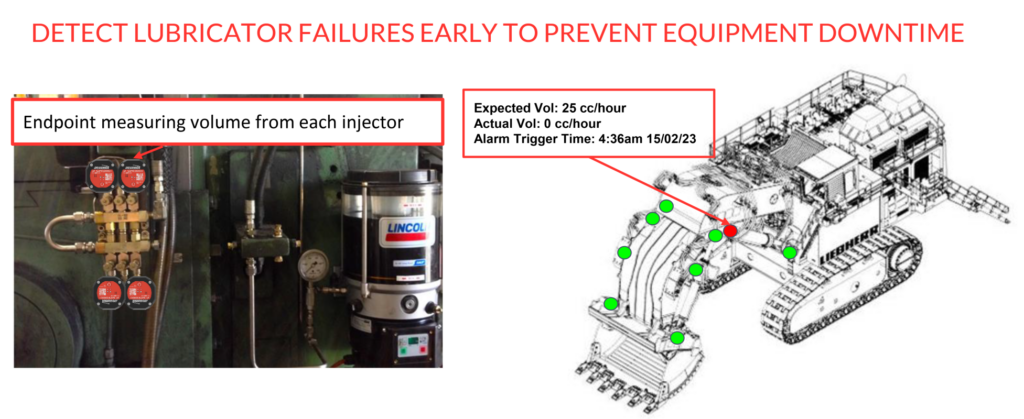
USE CASE 3 - PREVENT DRIVE SHAFT RELATED FIRES
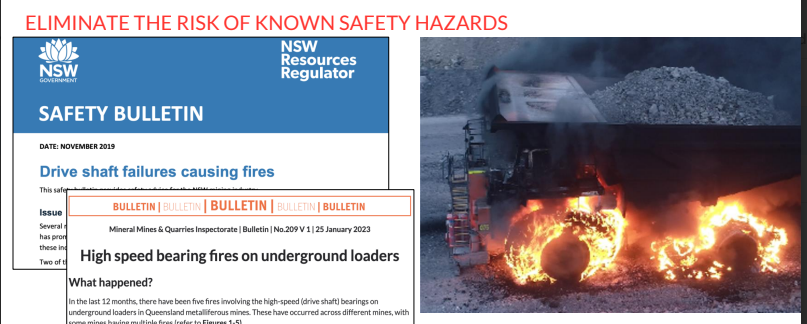
USE CASE 4 - FIXED PLANT GREASING
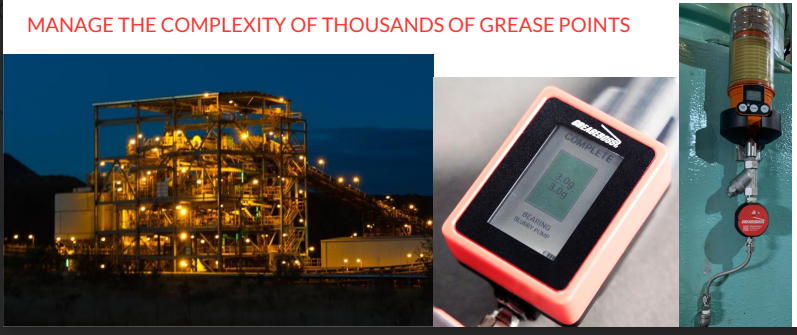
KEY BENEFITS
BENEFITS TO CASTROL
- Do more with less
- Better service - limited resources
- Provide higher level of service
- Proactive servicing - awareness of issues as they
arise, in real time - Lead the industry in digitising lubrication services
- Proactive servicing - awareness of issues as they
- Improve operational efficiency
- OPEX not CAPEX
- - Assets all managed by GreaseBoss
- Reduced safety risk
- Minimise time on the road
- Eliminate climbing over equipment for inspections
- Reduced contamination
BENEFITS TO CUSTOMER
- Value add in service contract
- Transparency with metrics
- Vertically integrated services with consolidated supplier
- All lubricant operational work handled under one contract
- Central management of key digital delivery projects
- Technology implementation
- Data & insightful metrics
- Expertise & scalability in technology implementation
- OPEX not CAPEX
- Eliminate safety risks
- Track onsite hydrocarbon usage
- Fuels and oils are currently tracked
- GreaseBoss provides the capability to track grease consumption
GREASEBOSS WITH CASTROL CUSTOMERS
CURRENT DISCUSSIONS
- Dawson Mine
- Dragline grease bin pilot (x8 Endpoints)
- Site visit scheduled 14th March
- Mackay Sugar
- Grease bin pilot planned (x2 Endpoints)
- High interest in full GreaseBoss system (ie. manual
system and Endpoints) - System proposal ready to send via Castrol
ADDITIONAL OPPORTUNITIES
- BHP WAIO
- Demonstrate system benefits leading into tender
- Bowen Basin
- Stanmore
- Anglo American
- Hunter Valley
- Other opportunities?
THE FUTURE OF GREASEBOSS
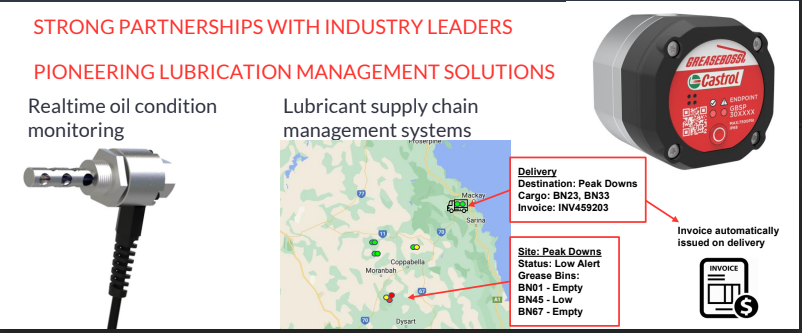